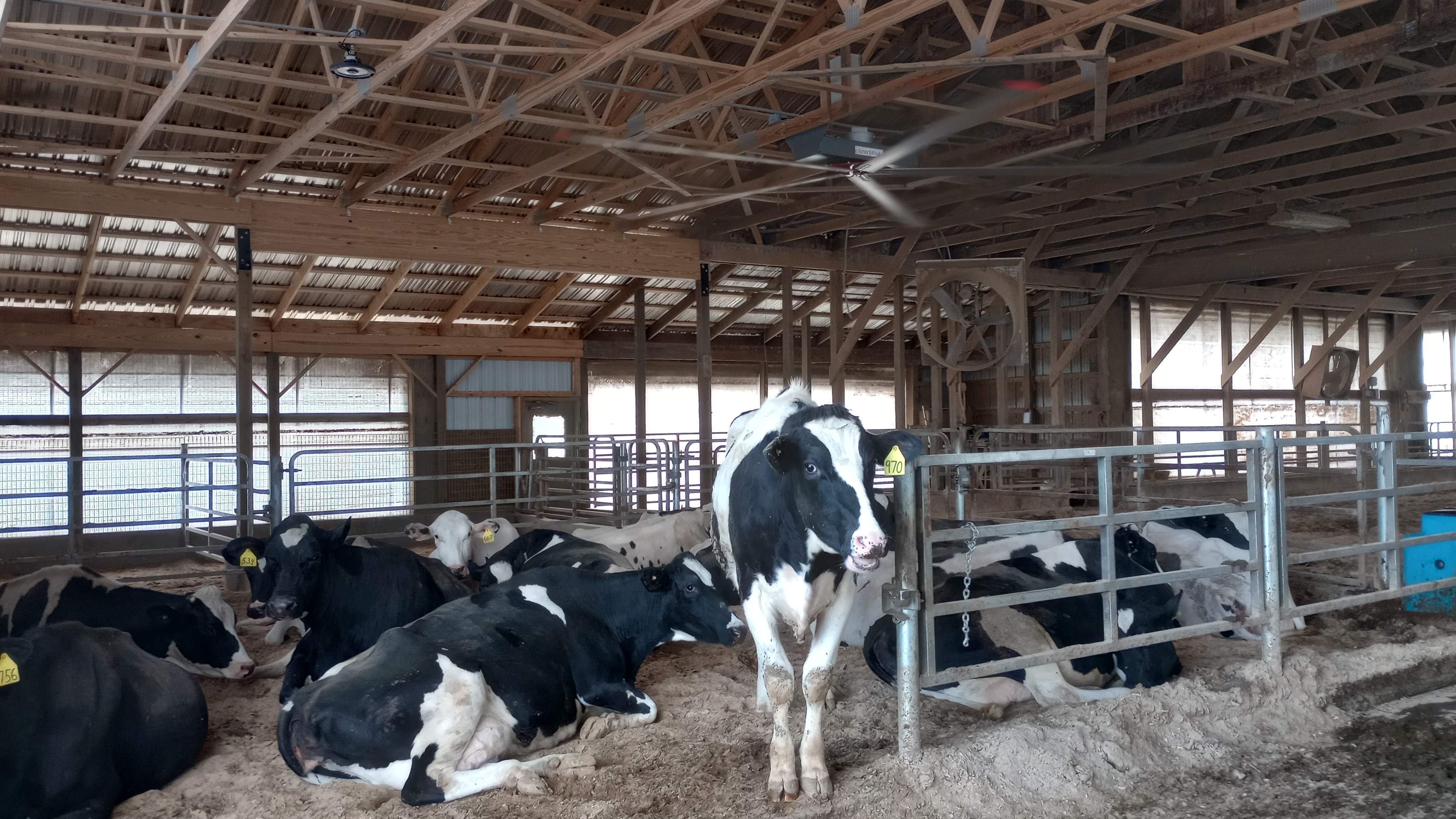
Fans and livestock ventilation. HVLS and panel fans
Ventilation is required in livestock barns to keep cows and other animals comfortable and productive all year.
Ventilation brings in fresh air and eliminates excess moisture. It also aids in the regulation of seasonal temperature changes.
A barn’s ideal ventilation system depends on the structure, temperature zone, and animal species housed.
A naturally ventilated dairy freestall barn, for example, may only require stirring fans on the warmest summer days, whereas a tunnel-ventilated poultry barn will require the system to run more frequently
The fan determines a ventilation system's overall energy efficiency and energy expenses. If you buy the least efficient type available, you might triple your energy costs and get less air production from the fan. Energy-efficient fans will save money on energy while also producing more air.
Not all fans are created equal
Fan efficiency varies substantially, according to laboratory measurements. High speed farm fan tests at the University of Illinois Bio-environmental and Structural Systems (BESS) Lab show that fan selection affects energy efficiency, operating costs, air output, and ventilation efficacy.
The majority of fans are graded in two ways:
- by the amount of air output in cubic feet per minute (cfm) at a given static pressure (in inches)
- by the amount of energy spent, or the watts of electrical consumption (watt)
Combining these two components yields a total fan efficiency rating: X cubic feet per minute per watt at X inches of static pressure.
A low efficiency fan, for example, will have a rating of 17 cfm per watt at 0.05 inches of static pressure. At 0.05 inches of static pressure, a high-efficiency fan will have a rating of 20 cfm per watt (or above).
Efficiency is affected by fan components.
Shutters and guards can restrict air movement and cause static pressure to build up. The use of a discharge cone, on the other hand, minimizes the static pressure of a fan.
Static pressure reductions can enhance energy efficiency by 12 to 23%, depending on fan size. Fans used for tunnel ventilation should have a diffuser to optimize energy efficiency.
The energy efficiency of a fan rises as its diameter grows. As a result, one huge fan uses less energy than two small ones. From a ventilation control aspect, having numerous fans that can be staged may be preferable; this arrangement will help you achieve a balance between energy efficiency and efficient control.
Motors for fans
Agricultural fans typically employ single-phase fractional horsepower (hp) motors ranging from 1/3 hp to 1.5 hp.
Most motor manufacturers need to disclose efficiency data for single-phase motors; therefore, efficiency is unknown until the motor is tested. Several businesses have recently launched high efficiency single-phase motors, increasing motor efficiency to 77 to 84 percent and reducing energy use for the same air production by 11 to 26 percent.
If your barn is wired for three-phase power and your fan motors are larger than one horsepower, you should investigate three-phase motors. Premium efficiency three-phase motors are more efficient (2–8%) than regular three-phase motors. Unfortunately, three-phase motors with less than one horsepower are challenging to find.
Fan settings
Environmental controls should be used to activate fans. Automatic control guarantees that fans are only switched on when they are needed.
Put the probes in a location of the barn that will measure the air temperature, but make sure they are safe from animals.
Set thermostats at progressively increasing degrees to represent growing heat loads for stage fans.
Select a ventilation controller that is suitable for damp environments.
Wind-fighting fans:
Choose the proper airflow ratio. The wind has an impact on fan performance. Most fans may encounter wind at some point, but you can reduce this conflict. Before installing fans, evaluate the prevailing wind direction and place fans on the barn's downwind side. Given the barn's location, this positioning is only sometimes possible. And, in many places, the wind direction is constantly changing.
Windbreaks can help, but growing trees or vegetation takes time and may need to be more viable or desired in specific locations.
Select fans with a high airflow ratio; fans with a high ratio are less impacted by winds than fans with low airflow ratios. The airflow ratio is calculated by dividing the airflow at 0.20 inches static pressure by the airflow at 0.05 inches static pressure. Airflow ratios for 48-inch fans range from 0.28 to 0.87, with an average of 0.74.
There is little association between the ventilation efficiency rating and the airflow ratio; while choosing a fan, consider both values.
Maintenance of fans
Any dirt that collects on the louvers, guards, grills, shrouds, or blades will restrict the air the fan circulates. Fan airflow can be reduced by 30 to 40% if louvers do not open easily or if dust accumulates on safety screens or grills.
To maintain efficiency, fans should be cleaned regularly. Clean the collected dirt from the louvers and lubricate them with a dry lubricant such as graphite to prevent dust and grime from adhering to them. Dirt on motors can cause them to overheat, resulting in a breakdown in motor insulation and a reduction in motor life.
If the fan's motor is completely encased and has a water-tight wire connection, you might clean it using a powers prayer. Loose belts can cause belt slippage, decrease airflow by up to 30%, and diminish belt life.
If the fan does not have an automatic tensioning device, you should check and re-tension the belts monthly. This maintenance task is rarely performed. As a result, most fan manufacturers provide V-belt self-tightening devices with new fans. Several of these devices can be retrofitted onto existing fans to cut maintenance costs and disruptions to ventilation.
Finally, if you have an emergency backup power or alternative ventilation system, test it regularly.
Fan selection
Discharge cone fans are more efficient than non-discharge cone fans. Motor efficiency affects energy consumption, while speed affects efficiency and noise levels.
Fan blade tip speeds exceeding 4,500 feet per minute will produce excessive noise. Fan revolutions per minute (rpm) should be fewer than 720, 480, 360, and 320 rpm for fan diameters of 24 inches, 36 inches, 48 inches, and 54 inches, respectively, to keep noise levels low.
Machete, straight and teardrop blade shapes are more efficient and collect less dust than cloverleaf-shaped fan blades.
The clearance between the fan blade and the housing affects the fan's efficiency and the static pressure at which it can operate.
Air will seep back through the fan blade and housing if there are large clearances. The smooth and rounded entrance of the housing to the blade reduces turbulence and drag as the air enters the fan blade airfoil.
Stirring fans are one type of fan. Stirring fans move air within a structure to keep it uniformly warm, eliminate dead zones, and enhance air velocity to keep animals cool.
High-speed fans are designed in a variety of ways. Some models include a motor with a blade attached to the motor shaft and a grill to protect the blades. Others are box-type, which include a shroud supporting the motor and blade (the same type fan found in tunnel ventilation, but without shutters or diffusers).
These box fans may or may not have a grill. High-speed fans are frequently put over the feeding alley or over the central cow beds in a dairy freestall barn to offer cooling.
Fans are typically positioned ten feet apart for every foot of fan diameter. As a result, 48-inch fans should be spaced 40 feet apart, but 36-inch fans should be spaced 30 feet apart.
Stirring fans are also extensively used in greenhouses and agricultural storage facilities to maintain constant temperatures and prevent condensation.
HVLS fans
Since the late 1990s, high-volume, low-speed (HVLS) fans have been used in the agricultural sector. They should be installed in high-ceilinged buildings, such as dairy freestall barns. HVLS fans are huge paddle-type ceiling fans with diameters ranging from 8 to 30 feet; HVLS fans with diameters of 16 to 30 feet are commonly used in dairy freestall barns.
The fans are horizontally positioned to push a column of air down to the floor. Because the floor impedes air passage, the air moves out from the fan in a radial pattern. These are the most energy-efficient fans on the market today. A 24-foot HVLS fan can move as much air as six high-speed fans while using only one-sixth the energy.
The fans in a typical four- or six-row dairy freestall barn are spaced every 35 to 60 feet over the cow beds depending on fan size. Further benefits mentioned by current owners include drier floors, fewer insects, fewer birds in the barn, and reduced noise.
HVLS fans include a variable speed controller for adjusting fan speed. During the cooler months, some dairy producers use slower-moving fans to keep the air from stagnating.
Opponents of this system are concerned that if the fans are placed down the feed alley, the air velocity above the cows will be too low to provide efficient cooling. Feed manger lockups, cows, and stall partitions all obstruct air passage from the middle of the barn to the building's exterior walls.
Misting systems
Misting water into the air or over the backs of dairy cows can improve ventilation cooling efficacy. Research has demonstrated that combining misting with stirring fans reduces heat stress significantly more than fans alone. These systems typically sprinkle water over the backs of cows for one to three minutes. The misting is then turned off for 12 to 25 minutes as fans help evaporate the water.
You need to employ fans to mist dairy cattle in humid weather, such as the summer months in Wisconsin.
Wetting the cow can aggravate heat stress rather than alleviate it if the water does not evaporate quickly enough.
REQUEST A QUOTE